Using DSM in Large Scale Aerospace and Defense Manufacturing
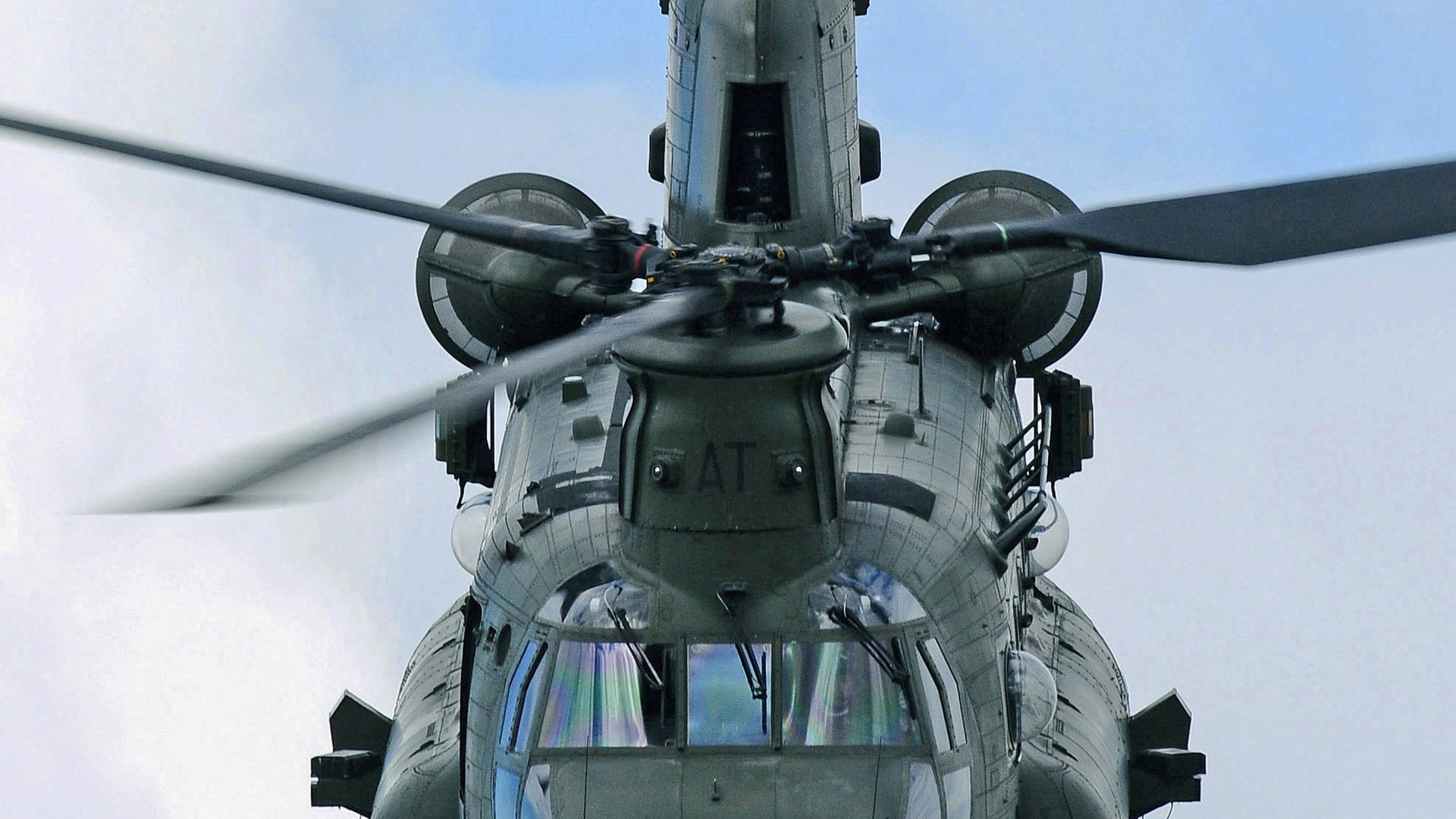
The Aerospace and Defense industry has a large problem with increasing cost and complexity in their projects. This is the result of Aerospace and Defense projects becoming larger and more sophisticated. To solve this problem, the complexity that has been introduced has to be identified, reduced, and managed. This will lower the overall cost and keep projects on schedule. As an example, Tesla puts a strong emphasis on modularity (reduced complexity) across all their hardware. So during the recent chip shortage, they were able to quickly switch to chips that were available and continue to make and sell cars with minimal disruptions. One technology that can be used to reduce complexity (and increase modularity) is the Dependency Structure Matrix (DSM).
How does DSM specifically help?
Many Aerospace and Defense companies including Boeing, Raytheon, and Northrop Grumman use DSM to model their actual manufacturing production process. They believe that detailed scheduling is nearly impossible without DSM. In this context DSM is used to perform the following actions:
- Defining dependencies
- Analyzing relationships
- Identifying weak points
- Prioritizing work
These actions in the DSM are used to identify, reduce and manage complexity. The inputs that these companies are using include things like:
- Factory Architecture
- Process Architecture
- Manufacturing Experience
- Task Sequence
- Manufacturing Constraints
The outputs from the DSM are:
- A baseline plan for the process
- A recovery plan for when there are disruptions or changes